Punch list management
Business sector: Engineering industry
Their inspections are performed by skilled technicians with the purpose of ensuring that products and processes meet the required quality standards across all the production stages right through engineering, testing, inspection, expediting, quality control and all related activities.
With respect to inspections performed on medium-sized and large-sized rotating machinery manufactured by their customer (specifically: gas and steam turbines, reciprocating and centrifugal compressors, centrifugal pumps, expansion turbines and valves), our customer attests that their goal is to guarantee high quality standards and to pre-empt issues previously detected in-the-field. With the help of a punch list, which itemizes flawed items detected on-site, in-depth inspections are therefore performed in manufacturing plants with the aim of spotting and dealing with non-compliance issues.

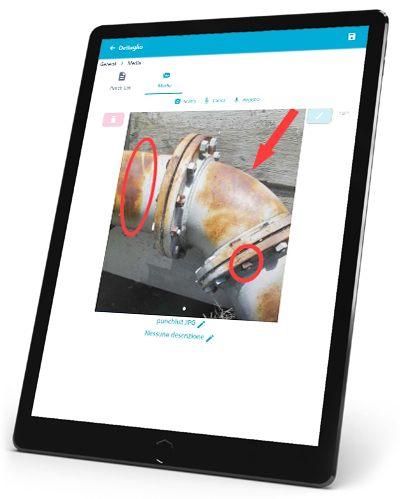
non-compliance issues in order to take corrective action.
The way our customer used to handle punch lists was admittedly outdated, as Excel spreadsheets used to be filled out completely manually and Power Point files were utilized to draw up inspection reports. Any image associated to reports had to be output from the field techs’ devices used on-site to a PC and then attached accurately to Power Point files, calling out each single image one by one. It is easy to see how inaccurate and time-consuming such a procedure must have been.
Soluzione
Solution
Orangedev’s long-term customer deemed it necessary to work out an agreed solution to enhance
functionality and to take a new approach towards streamlining the procedure for inspection reports. Thanks to the solution we have worked out, we now have new functions at our fingertips:
- Create a fully digitized inspection report using InspectionSite app, from data entry according to work orders to all applicable punch lists, that is documents listing work that does not conform to contract specifications.
- Compliance audit forms with automated photo capture are generated, listing detailed information relating to flawed items.
- Upon inspection completion, signed-off digital reports are issued, thus eliminating the need for hard copy printouts. No need to forward paper reports to inspection managers for sign-off.
- Implement effective audit trails over time.
- Once a form has been filled out, two files are generated by the system:
– A Pdf report with attached images documenting the inspection activity.
– A spreadsheet for data analysis, including condition indicators for faulty items. - Track the general trend of non-compliance issues with statistics dashboards.
Final results
Field staff and managing team are extremely satisfied with InspectionSite, as it has significantly streamlined the procedure for inspection reports and the punch list process.
Overall, significant improvement in time management and in inspection cost-effectiveness has been witnessed.
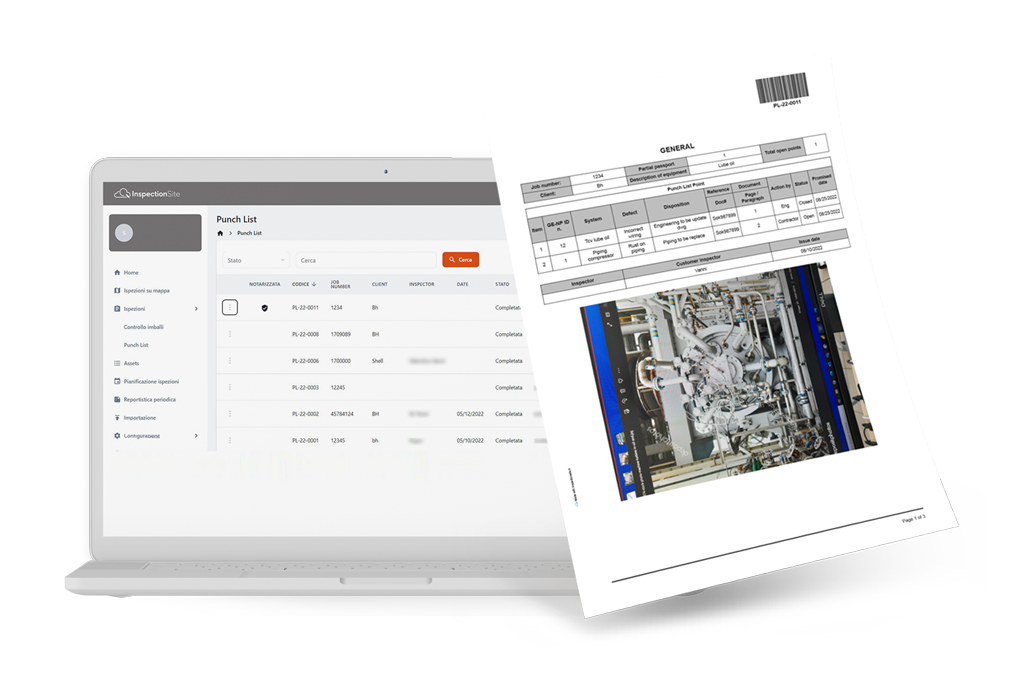