Inspections of packaging
for preservation control
Industry: Metal and mechanical engineering, Oil&Gas
A company that provides inspection services uses InspectionSite to perform
inspections on packaging stored in a warehouse, in order to guarantee its compliance over time.
Main activity
We have an important client who is a supplier of outsourced technical, inspection and business services and has over 20 years of experience in the international Oil & Gas and Power Generation industries.
In just a short space of time, it has extended the use of InspectionSite to the various types of inspection services required by its clients. One of these services is continuous monitoring of the packaging owned by the client and stored on the premises of a logistics provider. There are around 2,500 items of packaging on average and the service provides for their inspection every quarter. The purpose of the inspection is to identify any nonconformities and to take the necessary corrective actions promptly if any are found. In detail, the inspection consists of checking that the packaging is undamaged and that the external marking is correct, with a particular focus on the preservation expiry date for items to which special substances have been applied to protect them from damage.
Planning of the inspections and the human resources available to perform them is particularly important, as priority must be given to packaging close to its expiry date, in order to avoid oversights or delays in notifying this and thus failure to perform the necessary re-preservation activities. A specific check-list must be filled out for each packaging item during the inspection and then delivered to the client, accompanied by a photographic report.
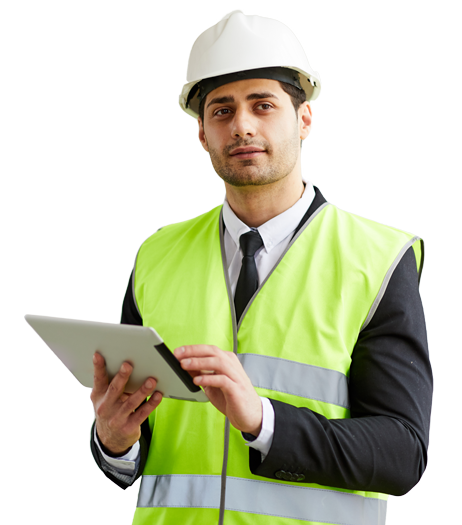
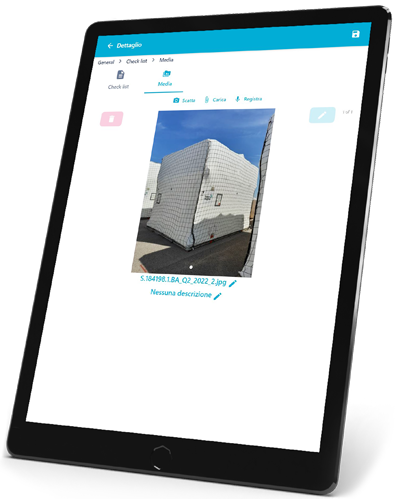
The inspection methods used before adopting InspectionSite
Before the introduction of InspectionSite, this process was managed with a large number of manual control activities on the packaging close to its expiry date and with preparation of the reports requested by the client.
- The list of items to be inspected was entered manually on an Excel spreadsheet, which was then shared with the client.
- The check-list had to be compiled as an Excel spreadsheet and compiling it directly on site, using a tablet or smartphone, was certainly not an easy task. The inspector filled out the check-list on paper in the warehouse, then went to the office and entered the data onto an Excel spreadsheet on a PC. The inspector then created the report starting from a Word file, had to print it out on paper, sign it and scan it for sending to the client.
- The photographic reports were created using an out-of-date tool with no dedicated repository for shared storage of the photographs and check-lists to be shared with the client.
- The reports prepared were sent only by e-mail, which made it impossible to share large quantities of photographic material easily.
Soluzione
Solution
In order to satisfy the client’s specific packaging inspection management and performance needs, we adapted InspectionSite to create a platform with the following functions:
- The inspections can be planned and assigned to the inspectors according to timetables monitored by the system
- An up-to-date list of the packaging items to be inspected is available on the dedicated web portal, simply by importing the Excel files extracted from the client’s ERP system.
- The system monitors the packaging and sends alerts for the items close to their expiry date, thus eliminating the risk of the inspection not being performed (InspectionSite as an asset management system)
- A mobile app is used to fill out the inspection check-list directly on site and directly to acquire the photos associated with the inspected item. This considerably reduces the time needed to fill out the check-lists and produce the photographic reports.
- It is also possible to record voice notes or draw on and add notes directly on each individual photo. Each photo can be marked with the packaging code, eliminating any identification errors.
- Geolocation of the packaging is also possible, allowing its position to be identified from the last inspection performed in the previous quarter.
- As an output, the system allows a report in PDF to be produced directly at the end of the inspection, with the check-list, photos and signature, for one or more items of packaging.
- All the information on the inspection is available online on the web portal. It is always up-to-date and can be consulted from any location.
- The list of packaging items to be inspected can be duplicated every quarter, based on the previous inspections, and a video comparison of the current inspection with the previous one on the same item of packaging is also possible.
- The client can also use a dedicated interface to access the report easily, after it has been validated and signed by the supervisors, meaning it is no longer necessary to send it by e-mail
Result
Use of InspectionSite has shortened inspection times by 50%, which means that double the number of inspections can be performed by each resource on the same day. This has allowed a better distribution of the workload, particularly at peak times in terms of the number of packaging items to be inspected.
The supervisors have also confirmed the benefits in terms of control and simplicity, as well as the shorter times for sharing the reports with the client.
Last but not least, there is no longer a risk of inspections not being performed due to oversights or human error, which guarantees 100% integrity of the stored material.
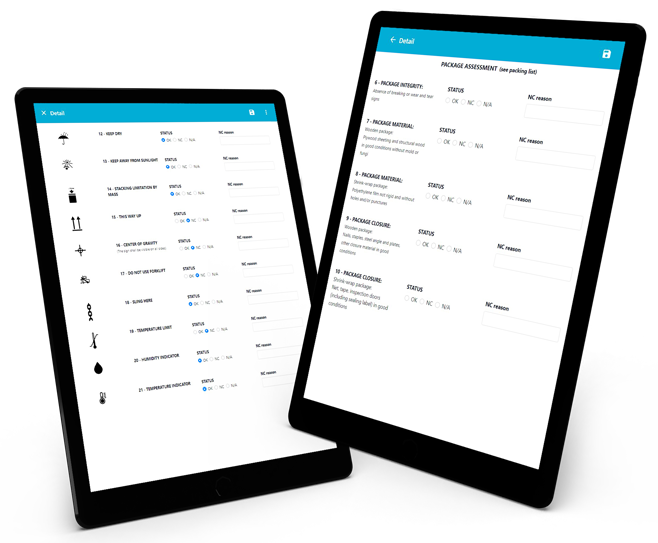
Key features
PhotoMark
Sorting and identifying pictures acquired during the inspection, quickly and without pairing mistakes. It is possible to mark each media with information, such as: article code, site name, date and time, GPS coordinates.
Sign
Inspector can upload and save his own signature from the APP or sign directly by the device touchscreen, allowing automatic creation of already signed reports, even in multiple positions or pages. It is also possible to acquire multiple signatures, in case reports need to be signed by various inspectors.
Compliance
It allows you to manage non-conformities in a simple way according to customizable criteria. You can easily see which inspections or individual items are non-compliant and track non-compliances even after their resolution.
Report
Report templates are totally customized according to your needs. Also large-sized and containing hundreds of photos output reports are managed and available in PDF, Word, Excel.
BigMedia
Storage of data and photos in original size without taking up space of company devices or storage. You can easily share them with customers/back oce or download them on local devices.
Import
Allows you to import data related to inspections to be carried out, in order to create reports with pre-filled information.
Mailer
Automatic mails to send copies of reports and/or media to customers or other recipients at the same time.